Likstenenpers retro’fit’
Lager energieverbruik, minder storingen en klaar voor condition monitoring
Over het verlagen van het energieverbruik wordt nog steeds voldoende gezegd en geschreven. Hoe relevant en zinvol het blijft, mag blijken uit de retrofit van een hydraulische pers voor likstenen. Dankzij de samenwerking tussen verschillende specialisten gebruikt de machine nu veel minder energie en is het aantal storing drastisch verlaagd. Een goede basis om een volgende stap te zetten richting condition monitoring en verdere verlaging van de onderhoudskosten.
Familiebedrijf Tromp uit Leeuwarden is ontwikkelaar, fabrikant en leverancier van mineralenmengsels voor vee. Een deel van de mineralen wordt samengeperst tot zogenaamde likstenen, die in heel Europa worden geleverd. De stenen hebben een gewicht van ongeveer 10 kg en vormen een aanvulling op het ruwvoer dat (rund)vee dagelijks krijgt in de vorm van bijvoorbeeld kuilgras, hooi, stro en snijmais. Op deze manier leveren de producten een bijdrage aan de gezondheid van de dieren en de kwaliteit van de melk en het vlees.
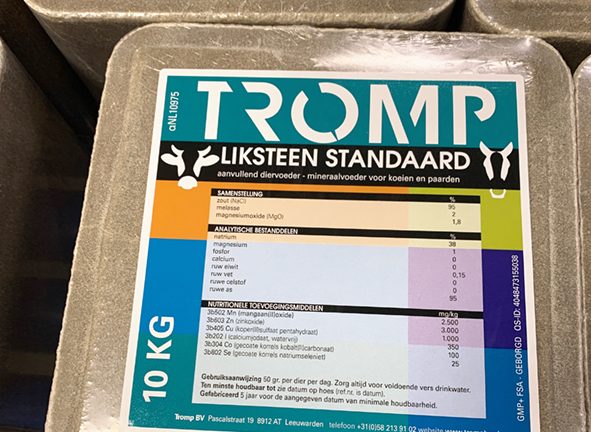
Een deel van de mineralenmengsels die familiebedrijf Tromp samenstelt, wordt samengeperst tot likstenen.
Zelf ontwikkeld en gebouwd
Tromp maakt de likstenen met een grote hydraulische pers die ruim 25 jaar geleden in eigen beheer is ontwikkeld en gebouwd. Het productieproces start met de aanvoer van losse mineralen in de juiste verhouding vanuit de mengerij. De grondstoffen worden gewogen en vervolgens in een persmal gestort en vervolgens niet aan één, maar aan twee kanten samengeperst. Hierbij loopt de druk dermate hoog op, dat de mineralen warm worden en aan elkaar smelten tot een solide blok. Dit samendrukken gebeurt met een kracht van 500 ton en levert volgens eigenaar Wiebe Tromp – derde generatie – het beste resultaat op. Tot slot worden de stenen uitgevoerd, nogmaals gewogen en via een transportband afgevoerd voor opslag of verzending.
Na 25 jaar produceert de machine nog steeds naar tevredenheid. Maar ook robuuste machines komen ooit in een stadium dat groot onderhoud nodig is en er een wens ontstaat om te moderniseren. Herman ter Schure is account- en projectmanager bij onderhouds- en servicebedrijf Perdok en geeft aan: “Onze mensen zijn al vanaf de ontwikkeling van de pers betrokken geweest bij deze machine en kennen deze dan ook van haver tot gort. Ieder jaar hebben zij het normale onderhoud uitgevoerd waarbij onder andere filters en slangen worden vervangen maarook schakelrelais. Daarnaast zijn er verschillende malen revisies uitgevoerd; onder meer aan de hydraulische pomp toen het aantal draaiuren of de uitkomst van olieanalyses daartoe aanleiding gaven. Het viel op een gegeven moment dan ook op dat er steeds meer storingen optraden en dat de gebruikte technieken verouderd raakten.”
Rechttoe-rechtaan
Het bedienen en instellen van de machine gebeurde bijvoorbeeld nog altijd handmatig. Daarbij was er maar één persoon in het bedrijf – de eigenaar – die de kennis en ervaring had om de pers op de juiste manier in te stellen wanneer er gewisseld werd van product. Daarnaast is er 25 jaar geleden vooral rechttoe-rechtaan ontwikkeld wat uiteindelijk leidde tot een behoorlijk overgedimensioneerde machine. Voor de kwaliteit van de likstenen is dat geen probleem; het energieverbruik komt hierdoor echter minder gunstig uit de bus. Het moment waarop besloten werd voor een retrofit, brak aan toen één van de perscilinders begon te scheuren en de machine steeds vaker in storing raakte. Jan-Dirk Kamminga is technical manager bij Perdok en vertelt: “Op dat moment moest een beslissing worden genomen: koopt of bouwt het bedrijf een nieuwe pers of is er voldoende reden voor een retrofit?”
In tweeën
Eigenaar Wiebe Tromp besloot voor het laatste: “Met de machine zelf is niets mis. Al het staal kan behouden blijven en met het vervangen van de diverse aandrijf- en besturingscomponenten was het mogelijk om de machine ver genoeg te retrofitten om storingsarm en energiezuinig verder te gaan.” Een inventarisatie van de mogelijkheden volgde en een plan werd geschreven. Hierin is de retrofit grofweg in tweeën verdeeld:
- Vervangen van oude componenten door nieuwe, energiezuinige varianten
- Digitalisering
Om bij de vervanging van componenten tebeginnen: de aanschaf van een nieuwe elektromotor heeft een belangrijke bijdrage geleverd aan de vermindering van het totale energieverbruik. Wim Tamminga was als application engineer Gears, Motors and Drives bij ERIKS betrokken bij dit deel van de retrofit. “Het klinkt vrij eenvoudig: het uitwisselen van de oude elektromotor door een nieuwe. Je kijkt naar het vermogen, kiest een nieuw type uit en omdat de spanning uit het lichtnet de afgelopen 25 jaar niet is veranderd, zijn er ook geen problemen bij de installatie ervan. Enerzijds klopt dit ook, anderzijds is het verhaal van Tromp illustrerend voor heel veel machines die in Nederland staan.
Machines die werken met elektromotoren die stammen uit de tijd dat typeplaatjes en IE nog niet bestonden. En natuurlijk kun je er terecht trots op zijn dat deze machines nog draaien, maar anderzijds ben je dief van je eigen portemonnee én lever je een ongewenste bijdrage aan de wereldwijde CO2-uitstoot wanneer je niet overweegt om over te stappen naar een energiezuinige motor.”
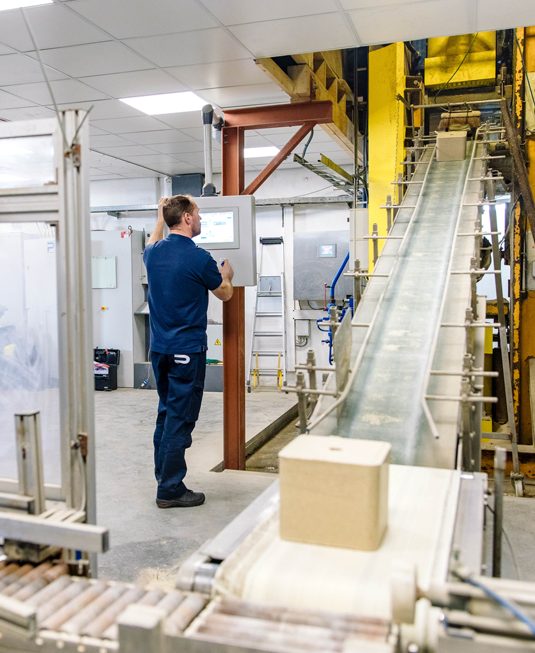
Na het samenpersen met een kracht van 500 ton worden de likstenen uitgevoerd, gewogen en verder getransporteerd voor opslag of verzending.
Keuze niet zo moeilijk
Het feit dat hier industriebreed nog steeds onvoldoende mee wordt gedaan, heeft volgens Tamminga in de meeste gevallen te maken met (een tekort aan) kennis en bewustzijn. “Dit bewustzijn ontstaat vaak pas nadat we hebben voorgerekend wat de vervanging van een oude elektromotor door een nieuwe variant met een IE klasse – het liefst 3 of 4 – betekent. Op basis van deze uitkomst is de keuze vaak niet meer zo moeilijk. Anderzijds zien we in de praktijk ook vaker dat in grotere bedrijven de budgetten verdeeld zijn. Heel flauw gezegd krijgt dan de afdeling die de investering in de elektromotor doet dan niet het voordeel van energiebesparing terug in zijn eigen cijfers, en dat lijkt mensen nog steeds tegen te houden om de investering te doen.”
Toch ziet Tamminga hierin wel verbeteringen: “Bedrijven laten vaker een berekening uitvoeren, of doen dit zelf via een online tool, en ook de wetgeving die energiezuinige elektromotoren uit een specifieke IE klasse verplicht stelt, helpt daarbij. Wanneer bedrijven bovendien aan de slag gaan met het optimaliseren van oude machines, blijkt vaak dat – net als bij Tromp – motoren veiligheidshalve flink zijn overgedimensioneerd. Door te berekenen wat de échte vermogensvraag is, kan de nieuwe elektromotor vaak een klasse kleiner worden gekozen en ook dáár zitten energiebesparingen. Eerlijk is eerlijk, deze kleinere, nieuwe motor gaat dan waarschijnlijk geen veertig jaar mee, maar de kostenbesparingen met betrekking tot het energieverbruik overtreffen dit nadeel ruimschoots. Het tegenargument dat je dan wel meer materiaal ‘weggooit’ is geldig, maar elektromotoren worden steeds meer en ook steeds verdergaand gerecycled, waardoor zij praktisch volledig als nieuwe grondstof zijn in te zetten.”
‘Geen discussiepunt’
Terug naar Tromp. Hier werd in eerste instantie uitgegaan van een revisie van de elektromotor met bijbehorende kosten van 1000 – 1500 euro. Een nieuwe elektromotor zou een investering van 3600 euro betekenen. Wiebe Tromp: ”Berekeningen gaven aan dat een vervanging van de motor door een exemplaar met hetzelfde vermogen – dus een 1:1 vervanging – zou leiden tot een besparing op de energiekosten van 2375 euro per jaar. Een terugverdientijd van ongeveer twee jaar voor een 55 kW motor die vervolgens misschien ook wel weer 25 jaar meegaat, lijkt me geen discussiepunt meer.”
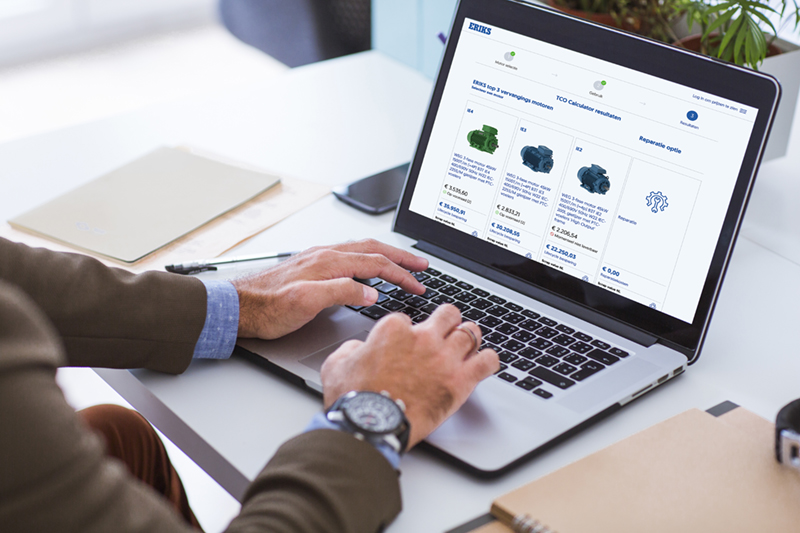
ERIKS heeft een online tool die de besparingen berekent bij vervanging van een oude elektromotor door een energiezuiniger variant.
Digitalisering
Een tweede belangrijke stap in de retrofit was digitalisering. Waar de machine voorheen volledig hydraulisch werd aangestuurd, is Tromp nu overgestapt naar een elektronisch regelsysteem van Rexroth. Dit systeem werkt met sensoren en meet onder meer de hoogte van de pers, die afhankelijk is van de hoogte van de te produceren liksteen. De hoogte wordt teruggekoppeld via het closed-loop systeem naar de besturing, die deze vervolgens nauwkeurig in stand houdt. Verder zijn druksensoren toegepast waardoor de pers nauwkeurig en traploos is te regelen en Tromp kan afstappen van de twee instellingen ‘hoge’ en ‘lage’ druk. De pers volgt nu de gewenste ’S-Curve’ waarbij hij rustig op gang komt, snelheid maakt richting de liksteen en vervolgens beheerst afremt om tot slot de persslag te maken. Tijdens de persslag wordt de druk zover opgevoerd als nodig voor het specifieke product. Ter Schure: “Door deze druksensoren en de bijbehorende regeling is het mogelijk om steeds exact de druk beschikbaar te stellen die nodig is waardoor relatief veel energie wordt bespaard.”
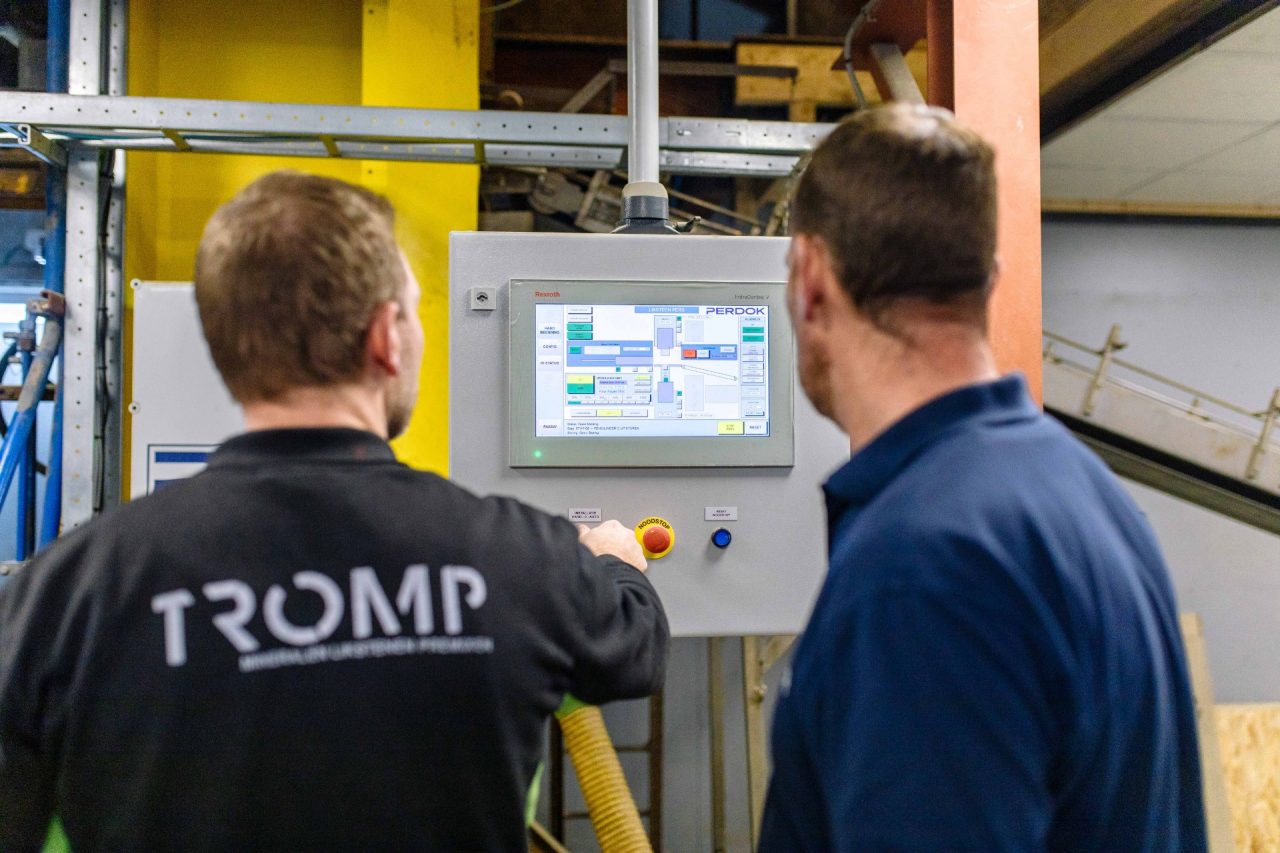
Het kiezen van het juiste recept en het starten van de pers is voldoende; de besturing doet de rest. Bediening is mogelijk via een app of het display.
Systeemdruk gereduceerd
Daarnaast is de proportioneel geregelde hydraulische cilinder voor het vullen van de mal vervangen door een elektromechanische variant. Deze uitwisseling heeft een aparte drukreduceer overbodig gemaakt waardoor er meer olievolume beschikbaar komt voor de pers. Door deze combinatie is uiteindelijk de systeemdruk gereduceerd van 200 naar 120 bar wat niet alleen leidt tot een significante energiebesparing meer tevens tot een lagere mechanische belasting van de machine."
Gebruiksvriendelijker
Tot slot is ook de autonoom werkende transportband voor de afvoer van de likstenen geïntegreerd. Dat betekent dat deze nu niet 24/7 draait, ongeacht of dit nodig is of niet, maar pas wordt ingeschakeld wanneer de pers produceert. Hiermee is het energieverbruik van het hele systeem nog verder omlaag gebracht. De energiezuinige machine als eindresultaat van de retrofit werkt naar volle tevredenheid. Onder andere omdat het aantal storingen drastisch is verminderd én omdat de machine vele malen gebruikersvriendelijker is geworden. Zo is bediening mogelijk via een app of display en is het niet nodig om fysiek naast de machine de juiste instellingen te maken. Het kiezen van het juiste recept voor de gewenste liksteen en het starten van de pers is voldoende; de besturing doet de rest.
Condition monitoring
Met deze retrofit is het project echter nog niet afgelopen. Met het oog op de toekomst zijn tevens diverse sensoren aangebracht die relevante parameters meten zoals temperatuur en oliereinheid. Door deze parameters te monitoren en te analyseren middels geschikte software, zal Perdok in de toekomst in staat zijn om op elk moment, en ook op afstand, de resterende levensduur van de machine of een specifieke component vast te stellen. De basis voor het zogenaamde ‘voorspellend onderhoud’. Voor dit traject wordt nauw samengewerkt met Bosch Rexroth. Sales director Arjan Coppens: ”Binnen ons bedrijf is inmiddels een compleet programma ontwikkeld waarin zowel de benodigde hard- als software is opgenomen om de conditie van machines te monitoren. Een dergelijk traject start vaak met wat wij noemen: een ‘Wellness screening for your machine’. Hierbij wordt een nulmeting verricht en gekeken wat de mogelijkheden zijn. Het uiteindelijke doel is het bereiken van een maximale beschikbaarheid van machines, minimale stilstand en tevens minimale onderhoudskosten.”
Klein én overkoepelend
Volgens Coppens is het mooie dat je deze aanpak zowel extreem eenvoudig en klein kunt toepassen als bedrijfsoverkoepelend en complex: “In het laatste geval heb je het dan over het verzamelen van heel veel data van uiteenlopende componenten en installaties en geavanceerde software om de analyses te maken, verbanden te leggen en conclusies te trekken. Daarbij is het overigens lang niet altijd nodig om grote hoeveelheden sensoren toe te voegen. Veel moderne componenten zijn door de toegepaste elektronica al langer in staat om data te verzamelen en beschikbaar te stellen. Denk daarbij aan elektromotoren of frequentieregelaars die automatisch informatie opslaan over het aantal draaiuren, de belasting, de temperatuur enzovoorts.”
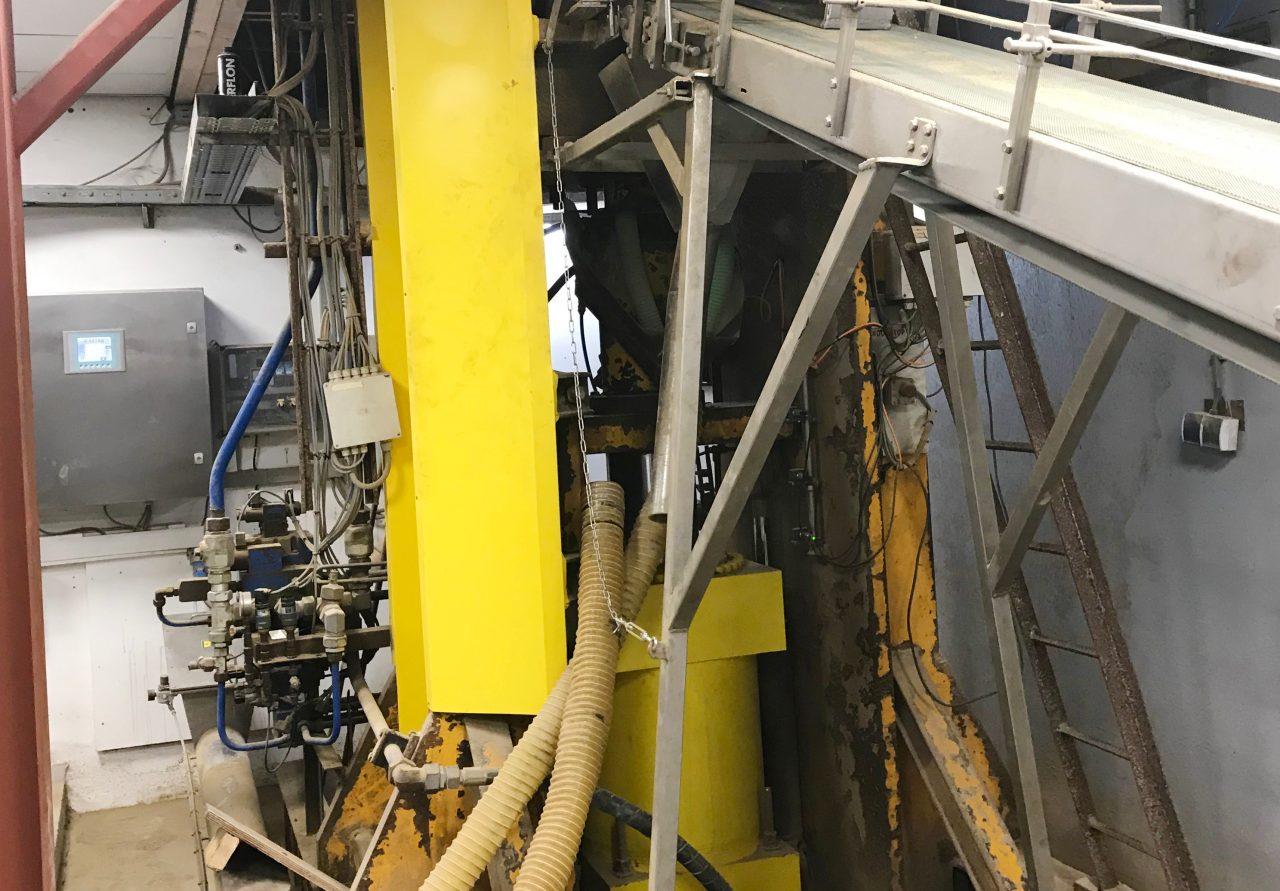
In de nieuwe situatie is de systeemdruk teruggebracht van 200 naar 120 bar.
‘Interessante tijden’
Voor hydraulische installaties – ook voor de pers van Perdok – zijn extra sensoren geplaatst om de kwaliteit van de hydraulische olie te monitoren. Daarbij gaat het vooral om de viscositeit en de aanwezigheid van vaste deeltjes die een belangrijke indicatie vormen voor enerzijds de conditie van de olie zelf en anderzijds afwijkende (slijtage)processen in de machine. Deze data zijn in te zetten om het hydraulisch onderhoud efficiënt te plannen. Wiebe Tromp: “Wanneer straks alles draait, kunnen we de exacte energiebesparing bepalen en ben ik ook benieuwd wat het ons oplevert in het kader van onderhoud. Interessante tijden!”
Dit artikel is eerder verschenen in Aandrijven & Besturen - april 2021
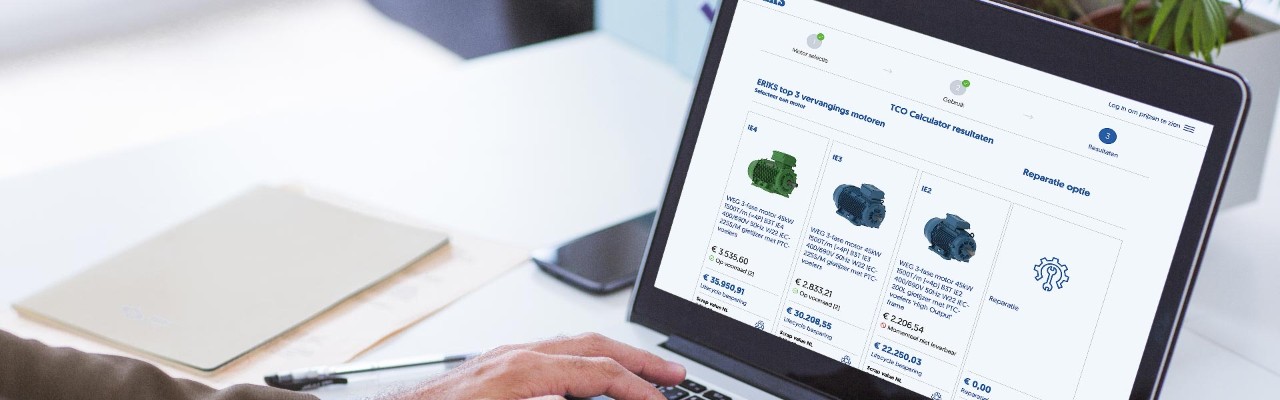
Bereken eenvoudig uw besparingen
Om uw energiebesparing en CO2-reductie bij de inzet van nieuwe elektromotoren te berekenen, heeft ERIKS een Motoren TCO-calculator ontwikkeld. Deze online tool geeft u na invoer van gebruiksdata, de meeste optimale elektromotoren op lange termijn. Dit is gebaseerd op aanschafkosten, energieverbruik en CO2-uitstoot. Zo kunt u uw sustainabilitydoelen bereiken en uw kostenbesparingen te realiseren. Weet u bijvoorbeeld dat de aanschafprijs van een elektromotor maar 2% van de Total Cost of Ownership (TCO) bedraagt? Wij hebben een grote voorraad aan hoog efficiënte (IE3, IE4 en IE5) motoren beschikbaar.
Gerelateerde artikelen
Wij helpen u graag verder
Know+How Hub
Blijf altijd op de hoogte met onze laatste blogs, nieuws en cases.
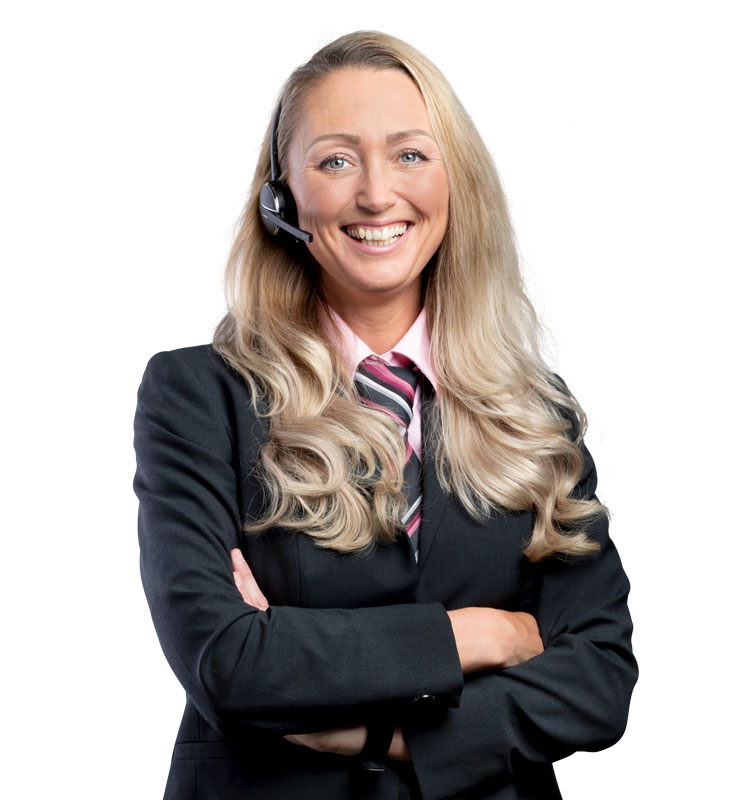