Mens blijft belangrijk onderdeel van predictive maintenance
Voorspellend onderhoud (predictive maintenance) wordt door velen geassocieerd met investeringen in hardware (sensoren en netwerken) en software. Maar het begint met duidelijke doelstellingen, een risico-analyse en gezond verstand. Hanno Spoelstra, portfolio manager voor smart asset management bij ERIKS, legt uit wat erbij komt kijken.
Condition based management, waar hebben we het eigenlijk over? "Met op toestandsafhankelijk onderhoud (condition based maintenance) ga je meten en inventariseren wat er aan de hand is met je asset, je bedrijfsmiddel. Je voert onderhoud uit wanneer de conditie van het asset daar om vraagt, net voordat falen optreedt. Waar het om draait is: in hoeverre kun je voorspellen wanneer het falen gaat plaatsvinden. Weet je dat minuten, uren, dagen, maanden, jaren van tevoren. Dat verschilt per type apparatuur."
Spoelstra, van huis uit werktuigbouwkundige, is sinds medio 2019 werkzaam bij ERIKS. Zijn vorige werkgever was SKF en daarvoor werkte hij bij IBM en Capgemini. Hij beschikt dus over een stevige onderbouw voor de mogelijkheden die IT het onderhoud kan brengen.
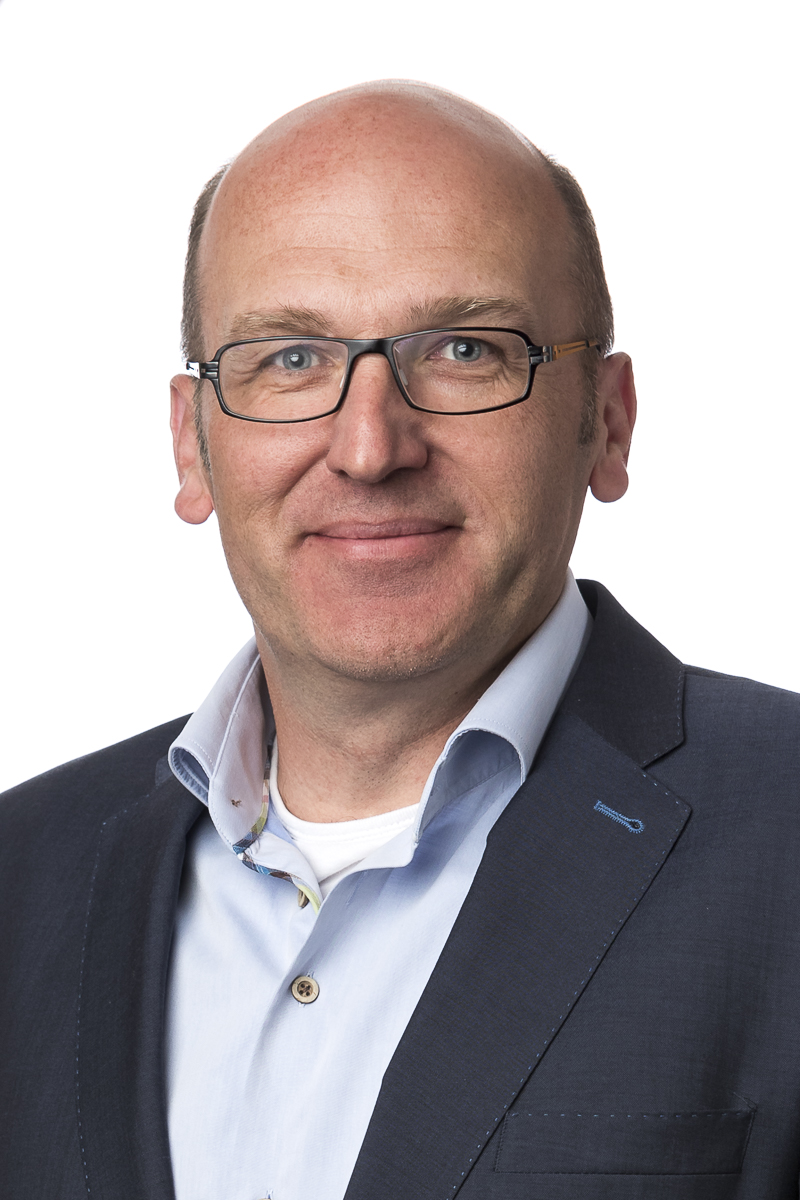
Hanno Spoelstra
Waarom predictive maintenance?
Spoelstra: "De doelstelling van predictive maintenance is om de risico's in de fabriek te beperken. Maar je hebt geen onbeperkte budgetten en mankracht ter beschikking. Je moet dus de assets die het grootste afbreukrisico vormen voor je productieproces – of voor de veiligheid van mensen, het milieu en de installaties – in kaart brengen. Die assets moet je meer aandacht geven dan onderdelen die niet kritisch zijn en bij falen geen gevaar opleveren. Ook het risico van stilstand moet je inschatten: wat kost een uur stilstand?
Je moet de reparatiekosten eveneens in de berekening meenemen. Als je iets tijdig repareert, hoef je maar één lager of één tandwiel te vervangen. Ben je te laat, dan moet je misschien een hele tandwielkast reviseren of vervangen. Verder kunnen standaard onderdelen snel beschikbaar zijn. Maar bij apparatuur die via 'engineer to order' is aangeschaft, kunnen er maanden overheen gaan. Dan wil je ruim van tevoren weten dat er iets aan de hand is. Je kunt kritische onderdelen op voorraad nemen, maar dat kost ook geld. Het wel of niet aanhouden van voorraden reservedelen is onderdeel van je onderhoudsstrategie."
Het voortraject
Er komt heel wat kijken bij het invoeren van een preventief onderhoudssysteem. Spoelstra: "Alles begint met een risicoanalyse. Voor je gaat investeren in hardware en software moet je op basis van de bedrijfsrisico's uitmaken wat de meest risicovolle machines en apparaten zijn. Daaruit bepaal je wat je gaat bewaken. Dat kun je doen met FMECA (Failure Mode Effect & Criticality Analysis) en dat soort methodieken. Dit kun je samen met onderhoudstechnici en reliability engineers doen, je kunt ook de hulp inroepen van bedrijven die dat dagelijks doen. Dat laatste is uit het oogpunt van compliance wel belangrijk."
Ook de overheid wil weten wat de risico's van een bepaald bedrijf zijn en hoe het die beheerst. Een bedrijf moet een analyse maken wat waar kan falen en wat daarvan de gevolgen kunnen zijn. Het moet bijvoorbeeld kunnen aantonen dat bepaalde assets dubbel zijn uitgevoerd of dat er conditiebewaking wordt toegepast. Ook moet het bedrijf in beeld brengen welke faalvormen in die apparatuur kunnen optreden en hoe het dat kan detecteren."
Als de faalvorm bekend is, valt te onderzoeken met welke sensor dat is te detecteren. Ongeveer driekwart van de faaloorzaken van roterende apparatuur is te detecteren door trillingsmetingen. Maar ook thermografie en ultrasoon zijn veel toegepaste technieken. Met ultrasoon is bijvoorbeeld lekkage van condenspotten te detecteren. En om cavitatie te detecteren, moet je niet met thermografie aan de slag gaan.
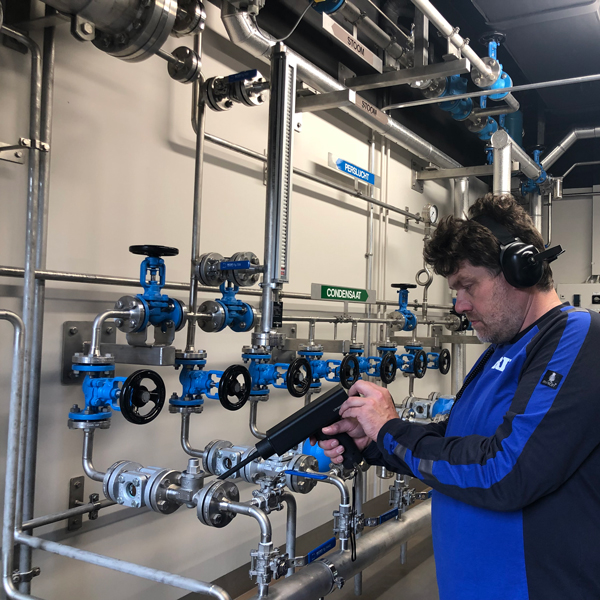
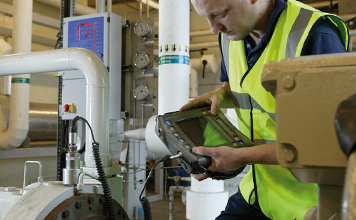
Bemonsterfrequentie
Vervolgens is de vraag hoe vaak en hoe snel een machine faalt. Daaruit is af te leiden hoe vaak data moet worden verzameld. Als er bij een gasturbine iets mis gaat, moet hij meteen worden uitgeschakeld. Als een dergelijke hoogtoerige machine stuk gaat, kan er een heleboel dure schade ontstaan. Maar bij een laagtoerige machine kan een maandelijkse meting al voldoende zijn.
Spoelstra: "De trend is belangrijker dan een actuele waarde. Je hoeft echt niet elke minuut zestig waarden te bemonsteren, tenzij machines snel kunnen falen. Dan moet je zeer frequent data ophalen en ook snel kunnen analyseren. Bij snel falende machines kun je met online systemen werken. Die systemen kunnen ook helpen voor machines die niet continu draaien. Je komt ze bijvoorbeeld vaak tegen in batchprocessen. Met online meting kun je dan data verzamelen op het moment dat de machine draait. Maar dan moet het een kritische machine zijn en moet je het belangrijk vinden om die data te verzamelen."
De kosten voor sensoren en het ontsluiten van data worden steeds lager, maar een hele fabriek uitrusten met sensoren kost veel geld. Wie met moeilijke omstandigheden zit, zoals ATEX-zones, heeft ook te maken met aangepaste dure bekabeling. Daarnaast moeten voorzieningen voor connectivity worden aangesloten, zoals gateways, routers of edge computers. Hiermee gaan de data van alle sensoren naar een centraal punt, waar al data sampling en thresholding mogelijk is. Vandaar kan een gebruiker data die interessant zijn, doorsturen naar de cloud voor verdere analyse.
Expertise
Trillingsdata leveren mooie 3D-grafieken op, maar wat zeggen die? "Je hebt een bepaalde expertise nodig om dat te kunnen analyseren. De laatste jaren investeren bedrijven veel in data-analisten, vaak wiskundigen of IT-ers. Maar zonder werktuigbouwkundige of elektrotechnische achtergrond kunnen ze zo'n signaal niet interpreteren. Je moet data in verband kunnen brengen met natuurkundige verschijnselen. IT speelt een rol bij het verzamelen en in databanken onderbrengen van data. Maar om ze te analyseren heb je de expertise nodig van werktuigbouwkundigen of anderen met een natuurkundige achtergrond.
Expertise kun je onderbrengen in algoritmes. Je kunt bijvoorbeeld een bepaalde frequentie correleren met onbalans in de machine. Een IT-er kan een algoritme schrijven om die logica te vangen. Als dat de enige anomalie is, weet je dat je de machine moet balanceren. Voor cases met meerdere fouten, zoals elektrische doorslag, onbalans en andere faalvormen heb je zeker expertise nodig", aldus Spoelstra.
Een bedrijf kan investeren om zelf die expertise op te bouwen, maar de vraag is of zo'n specialist een complete dagtaak heeft. Het kan er ook voor kiezen om dat uit te besteden aan gespecialiseerde bedrijven. Dergelijke bedrijven werken bijna altijd met cloud-oplossingen en ze brengen wekelijks of maandelijks een rapport en adviezen uit. Of ze schrijven een dasboard waarop de gebruiker zelf de toestand van zijn machines kan volgen. Spoelstra: "Een groot olieconcern bijvoorbeeld heeft een enorme installed base van raffinaderijen, chemische fabrieken en boorplatforms. Dan loont het om zelf die expertise in huis te hebben. Ook bedrijven als ERIKS en SKF hebben voldoende omvang om daarvoor mensen aan te trekken of op te leiden. Een probleem is wel dat er een chronisch tekort is aan dergelijke specialisten. Om er goed in te worden, moet je er ook fulltime mee bezig zijn. Je doet het er niet even bij, dan word je er nooit voldoende bedreven in."
"De huidige softwaretools kunnen steeds beter helpen. Maar je wilt voorkomen dat iemand op schermen kijkt en roept dat 'de computer zegt dat ……….'. Je moet de algoritmes die zijn ontwikkeld kritisch kunnen toetsen. Je moet bij een bepaalde melding zelf kunnen beoordelen wat er aan de hand kan zijn. Dat is misschien wat anders dan wat de computer zegt. West-Europa heeft sowieso een tekort aan technisch personeel, maar zeker aan mensen met deze expertise."
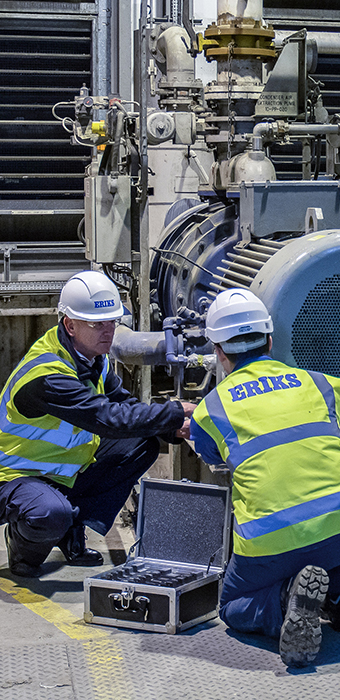
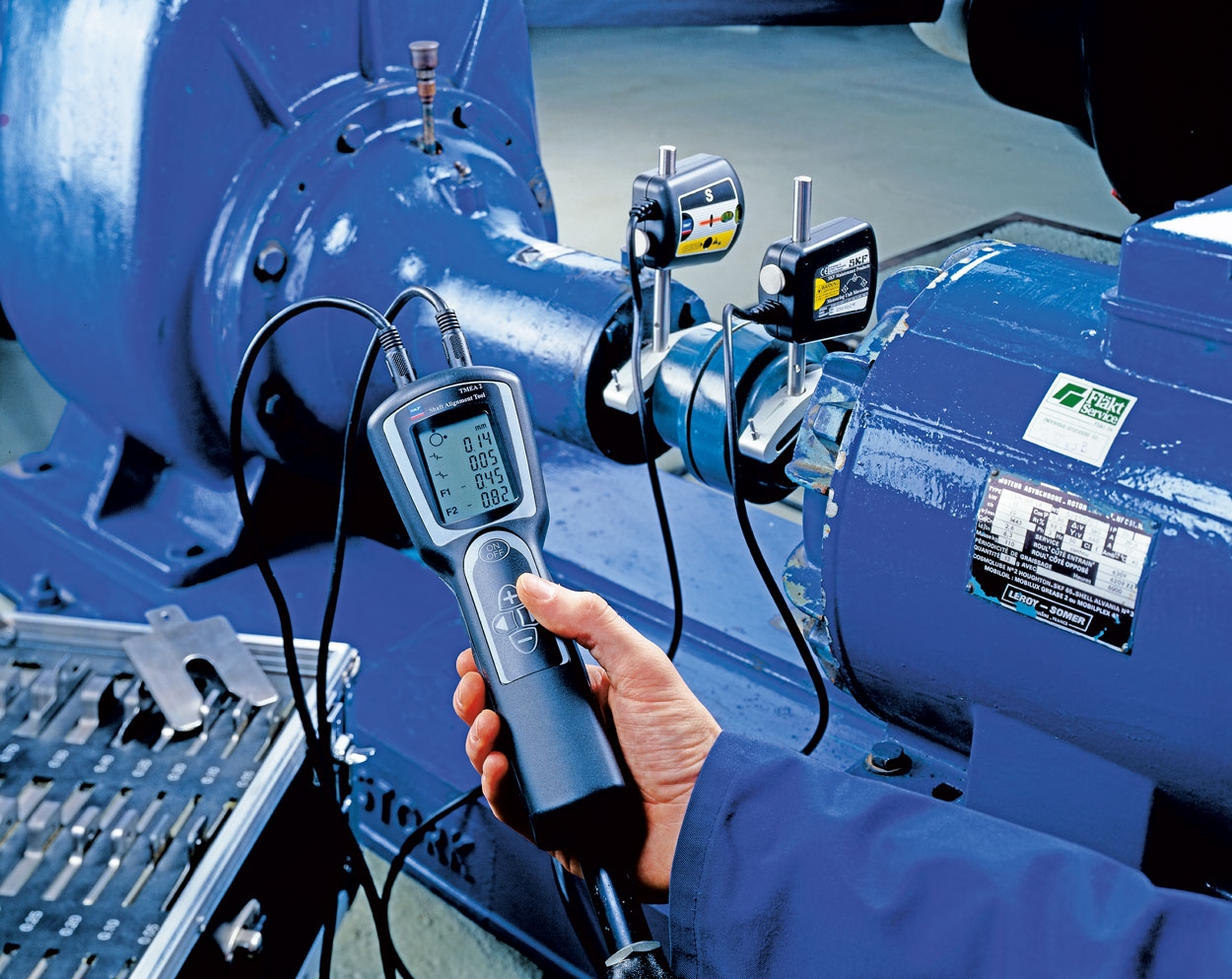
Startpunt van predictive maintenance
Wie wil beginnen met predictive maintenance heeft proceskennis en een risicoanalyse met bijvoorbeeld FMECA nodig. Spoelstra: "Je moet je steeds afvragen: als dit onderdeel of die machine uitvalt, wat gebeurt er dan? Ik heb een klant met drie parallelle spoellijnen, die alle drie uitkomen bij één palletiser. Als die ene palletiser uitvalt, ligt alles stil. Dat is dus je meest kritische asset en die moet je zeker bewaken. Je kunt dan onderhoud uitvoeren op het moment dat het uitkomt. Maar als je weet dat bepaalde werkzaamheden elke maand terugkomen, kun je meteen die palletiser meenemen. Moet je daar dan ook condition based monitoring op loslaten? Je moet daar een balans in zien te vinden. Dat geldt ook voor componenten. Heb je één machine met een bepaalde elektromotor, of meerdere fabrieken met elk een heel machinepark met honderden dezelfde motoren? Dan kan het interessant zijn om te investeren in conditiebewaking en te analyseren of die motoren bepaalde functies goed aandrijven. Of dat bepaalde merken motoren beter of slechter functioneren dan andere, en waarom."
Het meeste geld voor predictive maintenance gaat in hardware en software zitten. Spoelstra: "Het mooie van cloud-oplossingen is dat je per maand kan betalen, in plaats van dat je moet investeren in dure software en lang bezig bent om dat te installeren. Je betaalt bij een cloud-oplossing voor het gebruik en als je het na een tijd niet gebruikt, kun je je abonnement opzeggen. Je kunt de kosten voor de software daarmee aanzienlijk verlagen."
"Het aanbrengen, installeren en configureren van sensoren en andere hardware kan in de papieren lopen, zeker bij ATEX-omgevingen. Ook de connectiviteit op locatie kan lastig zijn. Je kunt wel gebruik maken van 4G en 5G, of van LoRa of ZigBee en dat soort protocollen, maar je moet vooraf testen of je daar überhaupt connectivity hebt. Ook moet de hardware geschikt zijn voor die omgeving, bedraad of draadloos."
De bron van inspecties
Welke functionarissen binnen een bedrijf werken met een predictive-maintenance-systeem? "We moeten onderscheid maken tussen het analyseren van de data zelf en het omgaan met de informatie die daaruit komt. De trillingsanalist constateert bijvoorbeeld een onbalans in een as, maar dan moet de onderhoudsdienst daar ook wat mee doen. Dat kan leiden tot een spanningsveld tussen onderhoud en werkvloer. Je kunt conditiebewaking gebruiken om de productieafdeling te informeren. Je moet kijken wat de consequenties kunnen zijn. Als de productie op volle kracht doorgaat en een apparaat of machine stuk gaat, kun je misschien een hele batch weggooien. Iemand zal moeten beslissen om wel of niet te stoppen."
Leveranciers van hardware en software verkopen het liefst zo veel mogelijk sensoren, netwerken, edge computers en softwarelicenties. Spoelstra maakt daar een kanttekening bij. "Ik heb in 2017 input gegeven voor een onderzoek van PWC en Mainnovation in de Benelux. Het gros van het ophalen van data ten behoeve van predictive maintenance bleek te gebeuren door mensen in het veld met een meetapparaat. Laatst deed men een online poll tijdens een webinar om dat onderzoek te updaten. Toen kwam ook naar voren dat visuele inspecties in combinatie met mobiele meetapparatuur nog steeds de meest toegepaste vorm is van het verzamelen van data voor predictive maintenance."
"Ik heb daar zelf ook voorbeelden van gezien. ERIKS doet bijvoorbeeld surveys van condenspotten, meestal eens per jaar. We hebben gezocht naar sensoren die konden detecteren of die potten lek waren. We vonden er één en die kostte meer dan het honderdvoudige van de condenspot zelf. Machines die niet snel falen en die minder kritisch zijn, moet je daar niet mee uitrusten. De technologische ontwikkelingen gaan verder, we zullen steeds minder mensen in fabrieken hebben die allerlei inspecties uitvoeren. Maar predictive maintenance is ook de man in het veld die met een thermografie- of ultrasoon apparaat metingen verricht. Daar gebruikt hij ook zijn zintuigen: hij kijkt, hij voelt, hij ruikt. "
De rol van ERIKS
Waarom heeft ERIKS een apart team opgezet voor asset management? "ERIKS is bekend als industrieel dienstverlener en we hebben daarom veel kennis van de producten die we verkopen. Daarbij hoort ook: het kunnen analyseren van de toestand van het product en het adviseren over resterende levensduur. Wij zien dat onze klanten steeds meer behoefte hebben aan dergelijke expertise maar die zelf niet in huis hebben. ERIKS kan dat kosteneffectief organiseren omdat we dit voor meerdere klanten kunnen doen. Het is een uitbreiding van ons portfolio, naast de producten zelf", aldus Spoelstra.
Condenspotten zijn een mooi voorbeeld. Ze zitten in veel installaties, maar klanten weten soms niet eens dat er condenspotten in hun systeem zitten, laat staan wáár. Je hebt een expert nodig die er naar kan luisteren en uitspraken kan doen over montage, lekkage en energieverlies. Dat laatste betreft niet alleen geld besparen, maar ook CO2-uitstoot reduceren.
Het gaat vooral om onderdelen voor machines op functioneel niveau. "Een pomp bevat altijd een lager en trillingen daarin zeggen iets over de hele installatie. Cavitatie, een kromme as, droogloop en elektrische doorslag kun je terugzien in het trillingspatroon. Je gaat geen sensor op een O-ring van een paar dubbeltjes plakken, dan wordt hij veel te duur. Maar slangen bijvoorbeeld moeten uit oogpunt van compliance jaarlijks worden gekeurd. Dat is ook een vorm van bewaking: je voert een druktest uit, net zoals je doet wanneer een slang nieuw wordt afgeleverd. In combinatie met een visuele inspectie op beschadigingen zoals scheuren of uitdroging kun je beoordelen of de slang nog goed is of moet worden gerepareerd of vervangen. De mens blijft een belangrijk onderdeel van predictive maintenance."
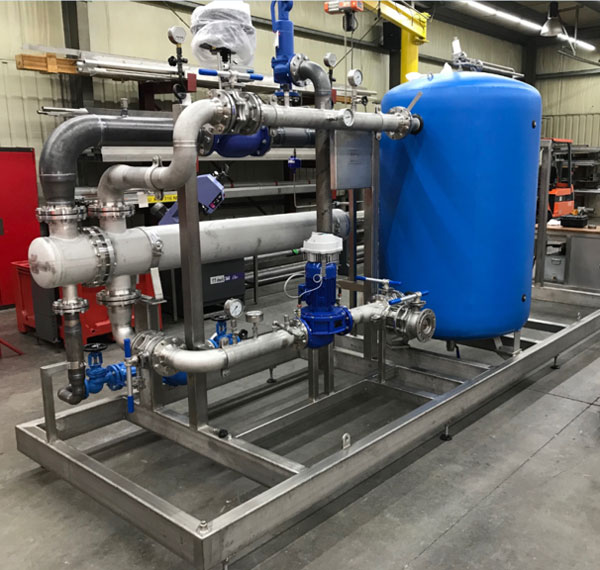


Contract monitoring
In welke vorm levert ERIKS deze dienstverlening? "We doen het wel ad hoc, maar we zijn druk bezig om daar contractvormen voor op te zetten. Je moet preventive maintenance voor een aantal jaren opzetten. Pas als je een trend ziet, kun je bepalen wanneer onderdelen of machines aan onderhoud of vervanging toe zijn. Je moet dus een langer lopend contract hebben om de ontwikkeling van een installatie te kunnen beoordelen. Wij hebben een groot project verworven voor alle afsluiters op een terminal. Dat soort orders is ideaal om daar ook deze service bij te leveren. Als wij afsluiters afleveren, worden ze gemonteerd en getest en met testcertificaat afgeleverd. Dan hebben we meteen een nulmeting."
Dit artikel is eerder verschenen in het vakblad Automatie PMA.
Meer informatie over predictive maintenance?
Gerelateerde artikelen
Wij helpen u graag verder
Know+How Hub
Blijf altijd op de hoogte met onze laatste blogs, nieuws en cases.
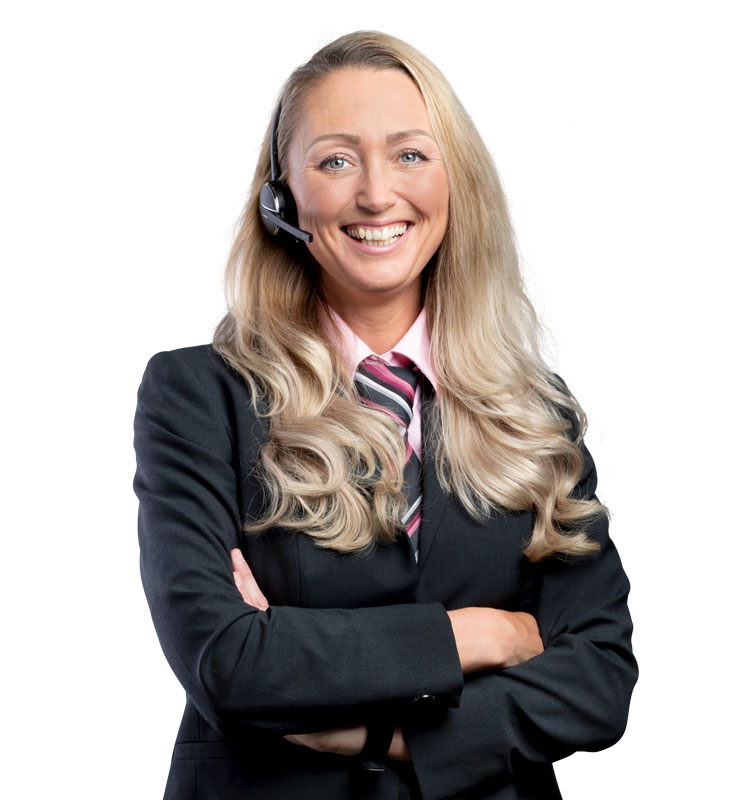