De juiste afdichting snel op de juiste plek
Decennia aan investeringen in afdichtings- en rubbertechniek betaalt zich uit
Oprichter Arie Eriks ging er al in de jaren veertig mee langs zijn eerste klanten in de zuivelindustrie: rubber afdichtingen. De afdeling Afdichtings- en Rubbertechniek van industrieel dienstverlener ERIKS heeft inmiddels 65 experts en een eigen onderzoekslab, waar afdichtingsmaterialen en -producten op maat voor de klant worden ontwikkeld en gemaakt.
Het is een mooi, nostalgisch beeld: Arie Eriks met zijn bakfiets, die door het Noord-Hollandse platteland ploetert om zijn klanten te voorzien van de juiste (rubberen) afdichtingen. Het beeld klopt wel degelijk, zegt Koen Scheppers, Sales Manager Sealing & Polymer Technology (voor de Nederlandse markt: Afdichtings- en Rubbertechniek). "Het is één van de zeven business units van ERIKS wereldwijd, maar was feitelijk ook de basis ervan."
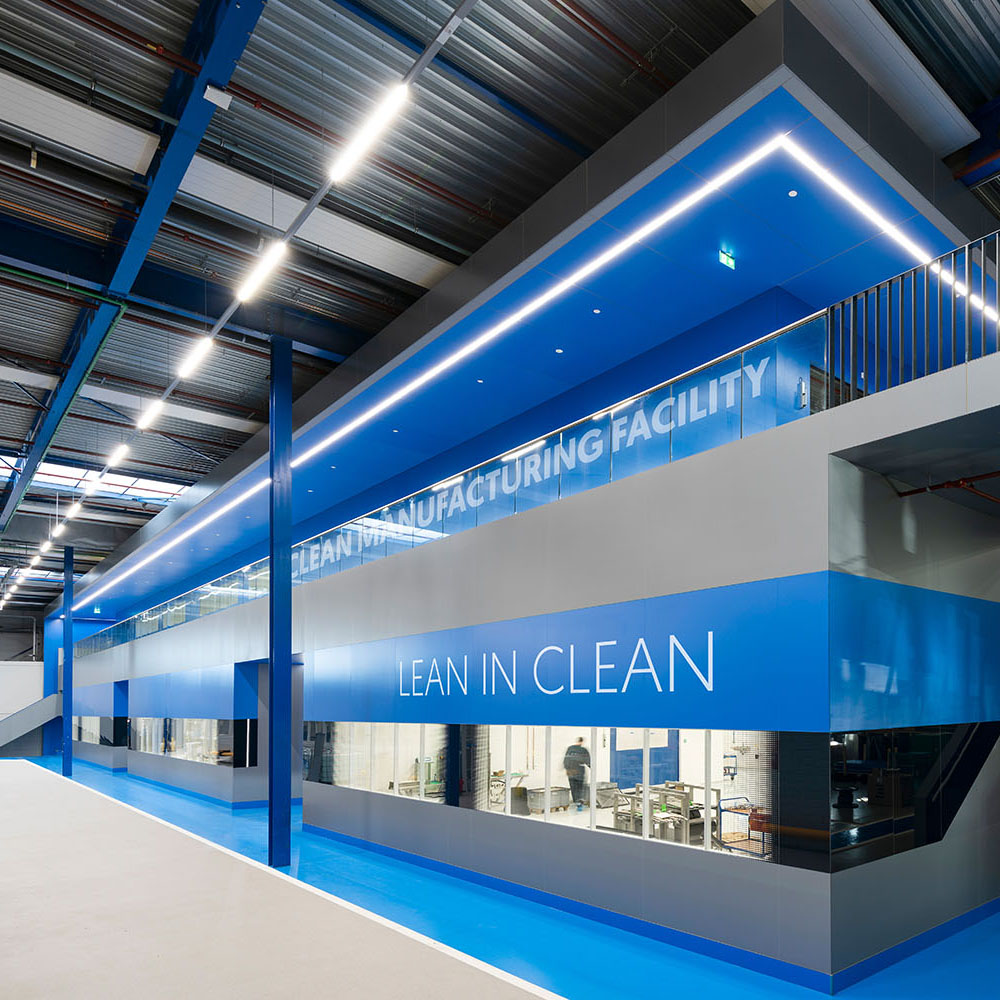
Afdichtingen voor OEM'ers en MRO'ers
In de loop van de jaren is niet alleen ERIKS zelf geëvolueerd tot een industrieel dienstverlener en multinational, ook het oorspronkelijke bedrijfsonderdeel is behoorlijk doorontwikkeld. "We hebben nu letterlijk tienduizenden producten op voorraad. En wat we niet hebben, kunnen we zelf ontwikkelen en maken. Bijvoorbeeld in onze nieuwe Clean Manufacturing Facility in Alkmaar, en anders bij onze vaste productiepartners in Europa en verschillende landen in Azië."
De afdichtingen variëren van O-ringen en rubberprofielen tot celrubberproducten en trillingsdempers. Daarnaast levert ERIKS onder andere afdichtingen voor dynamische toepassingen: oliekeerringen, hydraulische en pompafdichtingen. De afdichtingen worden bijvoorbeeld gebruikt door OEM’ers in de hightech (semiconductor industrie) en bij MRO’ers in de chemie en petrochemie, in de voedingsmiddelenindustrie, energiecentrales en offshore. Scheppers: "We leveren letterlijk aan alle sectoren van de industrie."
Veel geïnvesteerd
ERIKS, zo zegt Scheppers, heeft de afgelopen decennia heel veel geïnvesteerd in het opbouwen van eigen kennis en kunde. "En dat is succesvol geweest, want daardoor kunnen we nu elke afdichting haar eigen specifieke kenmerken meegeven. We maken uit een groeiende range materialen een product, dat bij haar toepassing aan specifieke eisen moet voldoen. Bijvoorbeeld waar het gaat om het functioneren onder hoge temperaturen, bij zware elasticiteit of onder continue spanning. Alleen door het juiste rubbermateriaal te gebruiken, kun je de juiste afdichting krijgen."
Want niet alle rubber is hetzelfde, wil Scheppers maar zeggen. Hij bedoelt: een rubber afdichting kan uit allerlei verschillende bouwstenen zijn geproduceerd. Hij heeft twee identieke rubberen stuiterballen: zwart en in omvang de grootte van een pingpongbal. "Ze zien er op het oog precies hetzelfde uit. Maar ze functioneren totaal anders. Als ik ze allebei laat vallen, zal de ene opstuiten tot aan het plafond en de andere voor dood op de grond blijven liggen. Je zult begrijpen dat het rubber in die balletjes ook heel andere eigenschappen heeft in een afdichting. Je kunt alleen maar goed met deze producten werken, als je weet hoe en wat die basiseigenschappen zijn en hoe die zich gedragen in de uiteindelijke vorm en toepassing."
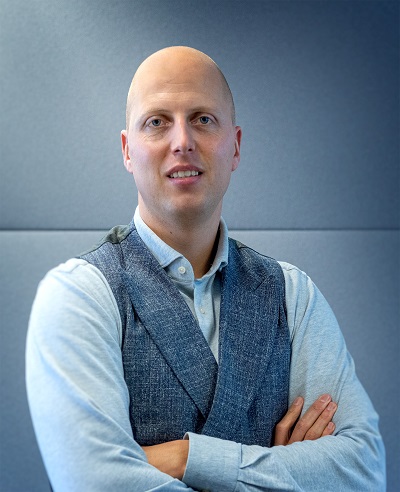
Koen Scheppers, Sales Manager
Sealing & Polymer Technology
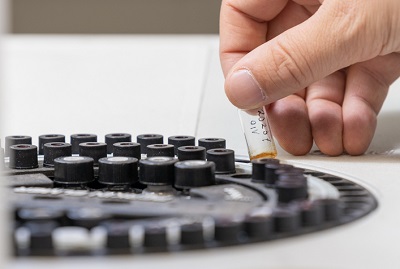
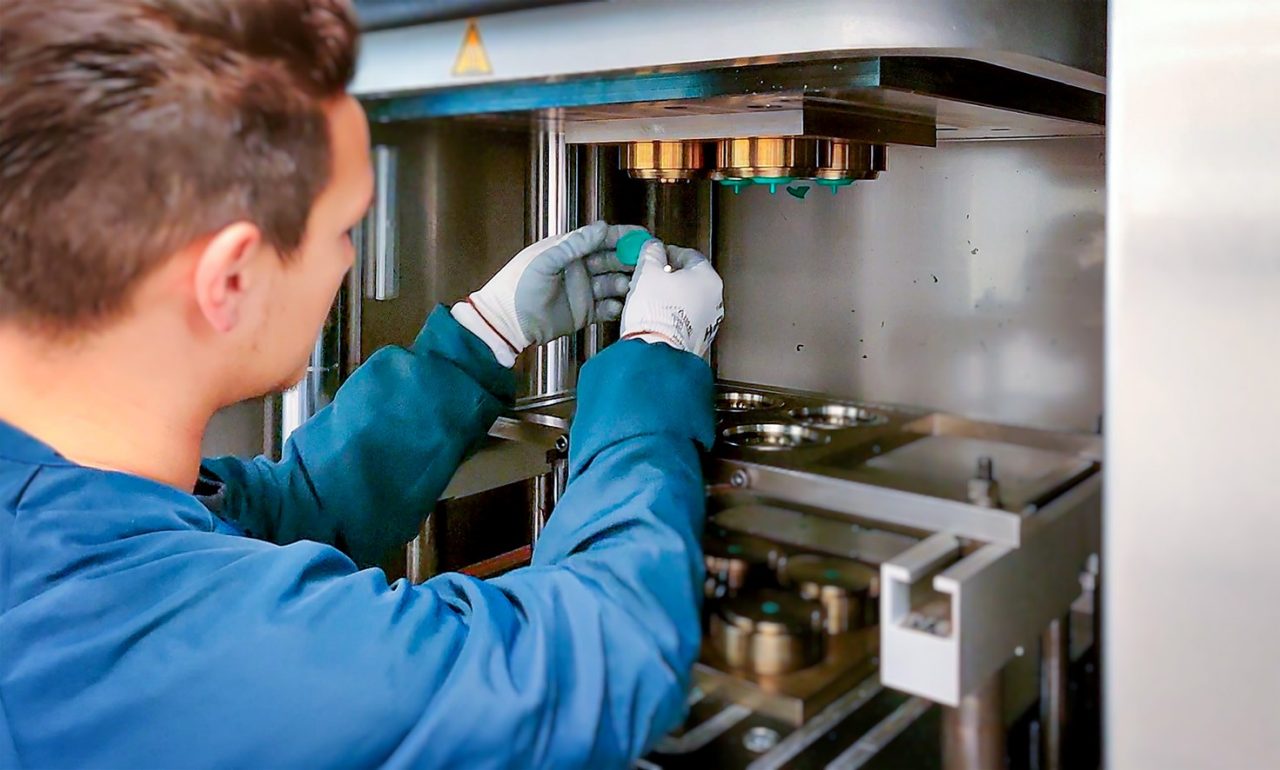
Testlaboratorium rubber
En zo komt het gesprek op ERT in Deventer. Oftewel: Elastomer Research Testing BV. Een volledig onafhankelijk ISO 17025 geaccrediteerd onderzoeks- en testlaboratorium voor rubber. Het bedrijf werd in 2012 onderdeel van ERIKS. Het is eigen laboratorium voor rubbertechniek, waar – voor derde partijen en klanten van ERIKS – rubber kan worden geanalyseerd en onderzocht. En waar onder andere ook trainingen en cursussen gegeven worden.
Scheppers: "We kunnen in het lab de fysieke eigenschappen van rubber afdichtingen analyseren en testen. Maar we kunnen er op verzoek van de klant ook nieuwe materialen ontwikkelen en produceren. De klant heeft bijvoorbeeld een nieuwe type afdichting nodig in een nieuwe machine. Welke kenmerken moet het materiaal hebben? Welke hitte moet het kunnen verdragen? Welke spanning? Hoe lang? Hoe zit het met de voedselveiligheid?
Op basis van de eisen kan ERIKS een rubbercompound samenstellen en intern produceren. En vervolgens in het laboratorium uitgebreid testen en controleren. Zo ontwikkelen we een product dat op papier al gevalideerd is; waarvan we officieel weten welke eigenschappen het heeft en aan welke eisen het kan voldoen. Vervolgens kan de klant het in zijn eigen omgeving de finale test geven."
Onmogelijk materiaal
Het laboratorium in Deventer verricht soms miraculeus werk, zegt Scheppers. "Op het gebied van voedselveiligheid zijn er natuurlijk vaak strenge eisen. En terecht. Voedselveiligheid gaat boven alles. Maar soms wordt dat wel heel ingewikkeld. Zo bepaalde de Chinese overheid dat er op een bepaalde plek reguliere ingrediënten voor rubbermaterialen in voedselmiddelentoepassingen niet toegestaan zijn. Eén soort rubber, FKM, is zelfs helemaal niet te realiseren binnen die restricties. En dat werd voor de collega’s van ERT de uitdaging: die afdichting te maken zonder die ene gangbare bouwsteen. En toch gecertificeerd te krijgen. Lang en technisch verhaal kort: het is ons gelukt. Veel zoeken, testen, ontwikkelen, proberen en weer testen: we hebben uiteindelijk een uniek materiaal geproduceerd."
En Scheppers heeft meer mooie voorbeelden van bijzondere producten die op verzoek van de klant gemaakt zijn. Zo was er een fabrikant van verwarmingsketels, die een afdichting nodig had op een plek in de productie waar giftige stoffen konden vrijkomen. "Er mocht dus onder geen enkele omstandigheid een lek ontstaan, want dat zou gevaarlijk zijn voor de eindgebruiker en tot zeer kostbaar onderhoud leiden. We hebben onderzoek gedaan en uiteindelijk een afdichting ontwikkeld, die we bij de klant langdurig en zes keer zo streng als de norm getest hebben. En die afdichter bleek, zoals we al hadden bedoeld, precies de goede oplossing."
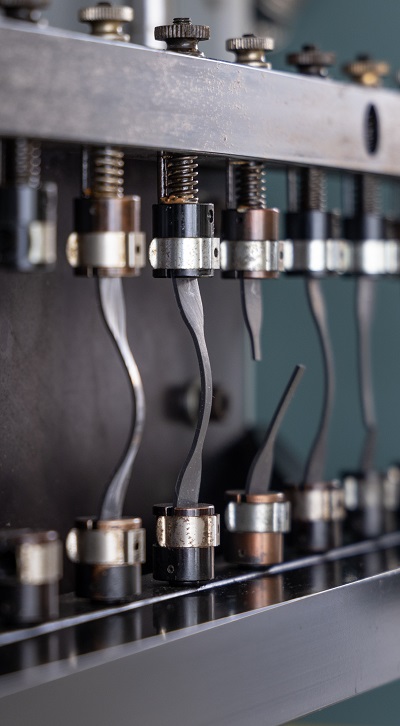
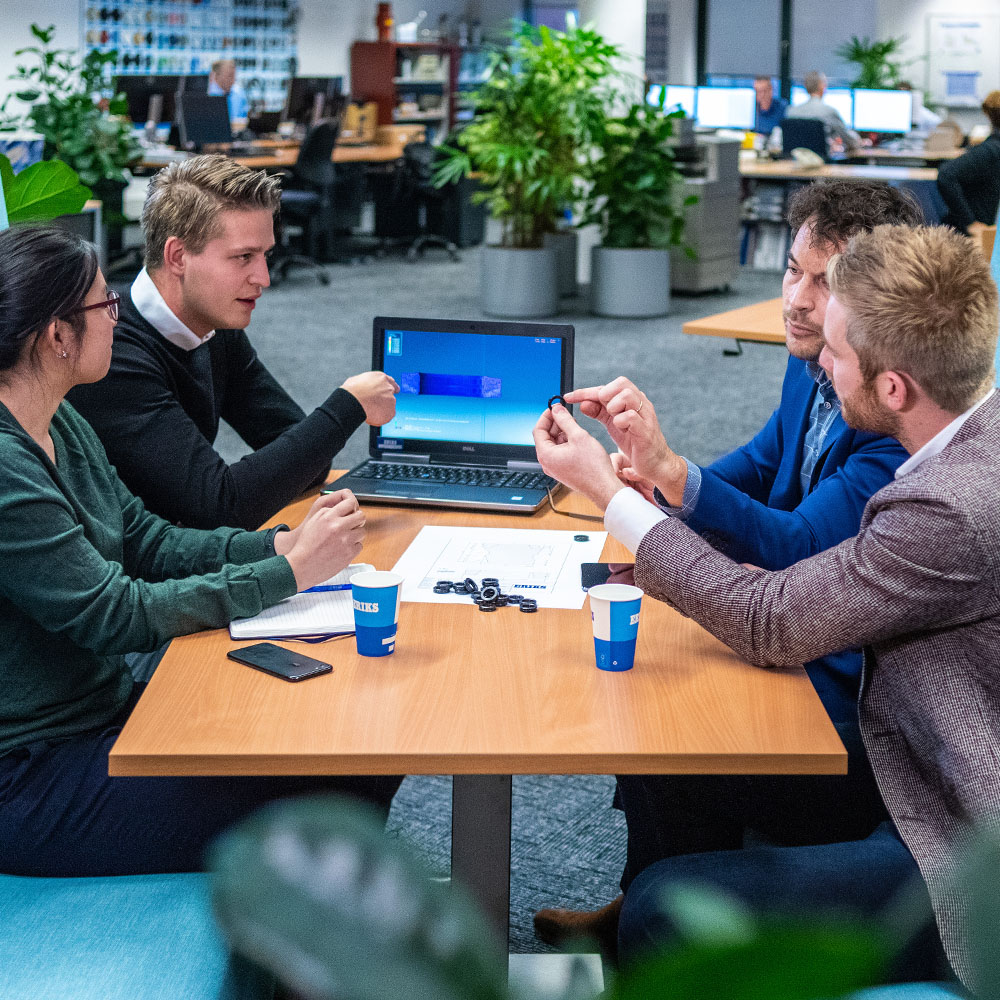
Vroegtijdig instappen
Deze voorbeelden brengen Scheppers bij een – in zijn ogen wezenlijke – boodschap aan de klanten: "Betrek ons zo snel mogelijk bij de ontwikkeling van nieuwe producten." En dat is niet alleen, zo zegt hij, omdat de doorlooptijd van dergelijke producten vaak lang is. "Want dat is waar, ja. Het ontwikkelen van nieuwe afdichtingen neemt veel tijd in beslag – zie de twee jaar in het voorbeeld van de ketelfabrikant. Maar het is niet de enige reden. Ik denk dat het ook belangrijk is, dat hoe eerder ERIKS bij productontwikkeling betrokken wordt, hoe eerder we onze kennis en kunde kunnen inzetten. Ga al aan de voorkant van het proces met ons om de tafel. Als we in dat proces goed samenwerken, betekent dat dat we eerder en sneller tot de juiste oplossing komen."
Scheppers komt met het voorbeeld van een klant die belde met de opmerking dat hij problemen had met verschillende pakkingen. Ze doen het niet, zo zei de klant, ze sluiten niet goed aan. "Dan gaan we kijken, op locatie en naar de tekeningen, en vragen we gedetailleerd door. Wat voor afdichtingen worden er eigenlijk tot nu toe gebruikt? En waar? Onder welke omstandigheden? Het bleek dat de gebruikte afdichtingen helemaal niet geschikt waren. Ze waren niet voor deze omstandigheden bedoeld – en functioneerden dus ook niet. Onze application engineers hebben onderzoek gedaan, betere versies ontwikkeld en de klant uiteindelijk een werkende oplossing kunnen bieden. Maar als de klant gelijk bij ons was gekomen, had hij al deze problemen niet gehad. Dan had hij direct de juiste afdichtingen geleverd gekregen, sneller, tegen lagere kosten. En had hij bovendien geen kostbare stilstand van de productie gehad."
Scheppers merkt ‘gelukkig’ dat steeds meer klanten de voordelen van deze werkwijze inzien. "Vaak moeten we eerst de brandjes blussen, zoals wij dat noemen. Dan worden we erbij gehaald als de klant of fabrikant een probleem heeft met zijn afdichtingen. En dan lossen we dat probleem natuurlijk zo goed mogelijk op. Gelukkig zet zo’n klant ons de volgende keer direct bij de ontwikkeling al met zijn ontwikkelteam aan tafel. Dan doen we mee vanaf het begin. En dat is voor beide partijen wel zo prettig."
Wereldwijde speler
ERIKS is een wereldwijde speler. Dat heeft ook wat de afdichtingen betreft een hoop voordelen, zegt Scheppers. "We hebben vestigingen, klanten én productiepartners op de verschillende continenten. We zijn bovendien natuurlijk eigenaar van de producten die we zelf ontwikkelen en produceren. Omdat we een innige samenwerking hebben met onze productiepartners, kunnen we overal ter wereld precies dezelfde variant van een bepaald afdichting leveren. Zo kunnen we voor onze klanten flexibel en snel produceren. En waar hij ter wereld zich ook bevindt: hij kan altijd van dezelfde producten worden voorzien. Dus voor hem in dat opzicht nooit verrassingen."
De productiepartners kunnen, vanwege hun grote capaciteit, indien nodig tienduizenden afdichtingen per maand leveren, vertelt Scheppers. ‘We kunnen dus altijd voldoen aan de wens van de klant.’ En mocht dat nodig zijn, dan kan ERIKS zelf op korte termijn kleine hoeveelheden afdichtingen produceren. ‘Wat we ontwikkelen en maken in Deventer, kunnen we onder hoogwaardige omstandigheden in onze Clean Manufacturing Facility in Alkmaar produceren. Op die manier kunnen we de klant in zijn eerste nood voorzien.’
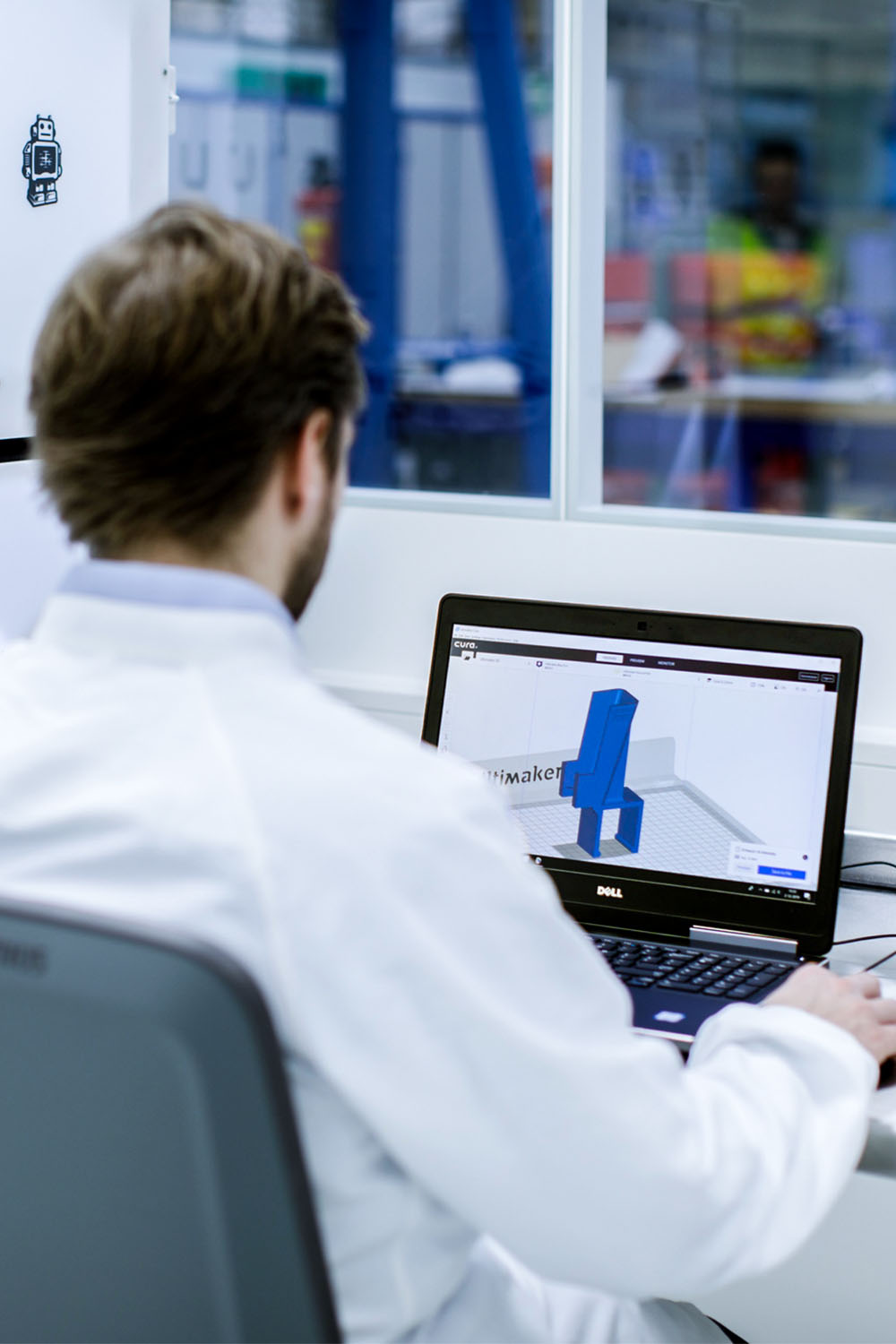
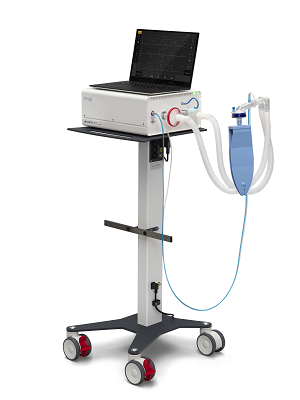
Beademingsmodules
De Sales Manager komt met een voorbeeld van deze werkwijze waar hij echt trots op is. De Nederlandse technologieleverancier Demcon was in coronatijd betrokken bij het ontwikkelen en realiseren van complete beademingssystemen die van levensbelang waren voor de vollopende IC’s. Voorafgaand aan de coronacrisis leverde ERIKS de afdichtingen voor het binnenwerk. "Ze hadden in eerste instantie slechts enkele tientallen nodig, maar moesten kunnen opschalen als de modules op grote schaal gemaakt zouden gaan worden. Dat was een uitdaging, want China was toen in lockdown en er werden geen afdichtingen geleverd. Toen hebben we zelf de matrijs gemaakt en de eerste afdichtingen zelf geproduceerd. In kleine aantallen, omdat we niet de capaciteit hadden voor grootschalige productie."
Daarmee kon Demcon alvast aan de slag. De productiepartners van ERIKS kregen ondertussen vanuit het hoofdkantoor Alkmaar de juiste specificaties aangeleverd en zodra de lockdown in China voorbij was, konden er tienduizenden afdichtingen ingevlogen worden. "Dat is het mooie van deze werkwijze. Met onze lokale quick supply-productie konden we de eerste opvang doen en vervolgens vanuit de supply chain de complete productie van de afdichtingen op snelle wijze laten invliegen. Demcon heeft tenslotte de beademingsapparaten binnen vier weken opgeleverd aan het ministerie VWS. Het was – en is – mooi om te zien hoe ERIKS snel en flexibel op alle fronten de benodigde kwaliteit kan leveren."
Dit artikel is eerder verschenen in Link Magazine #1 2021.
Brainstormen over de ideale afdichting, of uw ontwerp laten checken?
Laat de afdichting voor uw machine geen afterthought zijn. Het lijkt een klein onderdeel, maar de gevolgen zijn groot als u niet direct de juiste afdichting kiest. Wilt u een succesvolle machine afleveren zonder rework? Ga dan om tafel met één van onze specialisten en laat u in 30 minuten informeren over de juiste afdichting voor uw ontwerp. Wij staan vrijblijvend en kosteloos voor u klaar. Vraag hier uw adviesgesprek aan.
Hulp nodig bij de selectie van uw rubbermateriaal?
Vul het formulier in en we komen binnen twee werkdagen bij u terug.
Wij helpen u graag verder
Know+How Hub
Blijf altijd op de hoogte met onze laatste blogs, nieuws en cases.
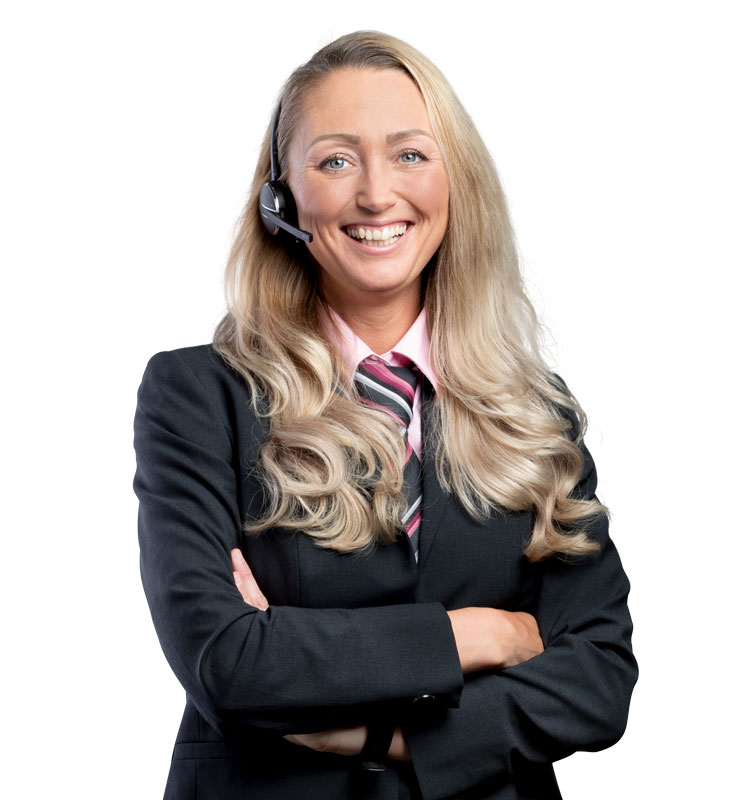